随着人们环境保护意识的加强、国家环境保护立法的完善、环境保护执法力度的加强,化学工业中剧毒、高污染化学品的生产与使用越来越受到制约。国家已经下令关闭了污染严重的小造纸厂、小印染厂;太湖流域关闭了一百多家小化工厂,淮河流域关闭了五百多家小化工厂,山东省关闭了1000多个污染严重的小化工厂。随着环境污染治理力度的加大,无三废、清洁工艺和绿色工艺日益受到人们愈来愈强烈的重视,业已成为化学家、化学工程师和化工企业家奋力追求的目标;对剧毒化学品的替代研究倍受重视。碳酸二甲酯就是在此大背景下应运而生的一种新的低污染泛用基础绿色化工原料。
近年来,碳酸二甲酯已成为化学化工科学家、企业家最热门的研究课题,国内从事这方面研究的单位有40多家,发表论文140余篇,对于工艺技术路线选择的观点相距甚远;多数文章认为甲醇氧化羰基化法投资小、成本低。鉴于我校对几个不同的工艺技术路线多年研究和转让九套工业化成功的经验,对碳酸二甲酯生产工艺技术路线作一个简要的分析,以供有志于该项目开发的科研、企业部门参考。
碳酸二甲酯的生产工艺主要有光气法、酯交换法和甲醇氧化羰基化法;光气法由于使用了剧毒的光气,产品质量差应用受到限制,且光气本身的使用也受到限制,己逐步被淘汰。
1.酯交换法
酯交换法是以碳酸丙烯酯或碳酸乙烯酯与甲醇酯交换反应生产碳酸二甲酯,同时联产丙二醇或乙二醇。碳酸丙烯酯是以环氧丙烷与二氧化碳合成的,碳酸乙烯酯则是以环氧乙烷与二氧化碳合成的。由此可以看出,酯交换法生产碳酸二甲酯的本质原料是二氧化碳和甲醇;环氧丙烷或环氧乙烷在过程中是一种载体,同时转化为丙二醇或乙二醇。由于丙二醇(乙二醇)主要是以环氧丙烷(环氧乙烷)水解而生产的;因此酯交换法过程的本质是二氧化碳与甲醇合成碳酸二甲酯过程(在热力学原理上是不能直接进行的)与环氧丙烷水解合成丙二醇过程的耦合。酯交换法生成碳酸二甲酯环氧丙(乙)烷与二氧化碳反应,经精馏脱除催化剂及轻组分获得高纯度碳酸丙(乙)烯酯,再与甲醇催化反应精馏,塔顶得到碳酸二甲酯与甲醇的共沸物,经分离得到碳酸二甲酯粗品,再精制获得高纯度的产品碳酸二甲酯;反应塔釜出来的物料,经精馏脱除轻组分甲醇循环使用,再经精馏得到联产品丙(乙)二醇,未反应完的碳酸丙(乙)烯酯循环使用。碳酸丙(乙)烯酯的单程转化率可以达到~99%。过程中的物料没有腐蚀性,设备基本上是碳钢的。建设一套年产10000吨碳酸二甲酯联产8400吨丙(乙)二醇的装置,在界区内设备投资2530万元,包括公用工程和铺底流动资金等总投资6508万元。氧丙烷水解生产丙(乙)二醇,环氧丙(乙)烷经过两级水解反应,经三效蒸发,精馏脱水、再精馏得到丙(乙)二醇,再经过两个塔回收二丙(乙)二醇和三丙(乙)二醇,环氧丙(乙)烷的选择性一般只有85%左右,资源浪费;由于过程中用到酸性催化剂等,大部分设备是不锈钢的,全套装置共有设备98台套。建设一套年产8400吨的丙(乙)二醇装置设备投资6000万元(进口设备15000万元)。从流程的比较可以看出,两个流程的投资相近;但前者可以生成两个产品,具有明显的优势,完全可以取代现有的丙(乙)二醇生成工艺,以解决国内每年13万吨丙二醇、146万吨乙二醇的缺口。从酯交换反应生成碳酸二甲酯的两个原料路线比较来看,环氧丙烷比环氧乙烷容易运输和贮存。为了提高环氧丙(乙)烷生产丙(乙)二醇的收率,可以环氧丙(乙)烷与二氧化碳合成碳酸丙(乙)烯酯,再水解生成丙(乙)二醇,可以降低能耗50%以上、提高收率10%以上,这一技术我们也已开发成功。
2.甲醇氧化羰基化法
甲醇、一氧化碳和氧气直接氧化羰基化合成碳酸二甲酯的方法又分为液相法、气相法和常压非均相法。
2.1液相法工艺
液相法工艺以意大利埃尼合成公司为代表;以氯化亚铜为催化剂,在100~130℃、2~3MPa下,在淤浆反应器中反应。首先甲醇、氧气和氯化亚铜反应生成甲氧基氯化亚铜,再与一该工艺过程是在一系列连续搅拌反应釜中进行的,氧气和一氧化碳物料压缩至反应压力后进入反应釜,同时向反应釜送人甲醇和催化剂,进行催化反应。未反应完全的一氧化碳和氧气从上部导出,进入第二反应器下部,液体物料则进入第二反应釜上部,同时补充新鲜氧气。以上述同样的方式进入第三反应釜反应,上部出来的气体进入冷凝器和分离罐,进行氧化碳反应生成碳酸二甲酯。气、液、固分离。冷凝液与气体挟带的液体及催化剂回流到反应釜中;气体则进入吸收塔除去二氧化碳。洗涤后的气体返回第一反应釜。第三反应釜下部流出的液体物料闪蒸至大气压,以释放出溶解在其中的气体,再经压缩机压缩循环使用。液体经过滤器过滤催化剂,再用甲醇洗涤,视效果情况决定催化剂再生还是循环使用。滤液送到分离回收工段,经分离获得产品碳酸二甲酯,分离出的甲醇循环使用。甲醇的单程转化率在32%左右,选择性按甲醇计近100%。按CO计不稳定,最高时92.3%,最低时仅60%。设备腐蚀性大,催化剂寿命短。
2.2气相法工艺
气相法与液相法的化学原理相同,它采用的是固体催化剂、在固定床反应器中反应;以美国DoW化学公司为代表,其催化剂为浸渍过无水氯化铜的活性炭,并加入氯化钾、氯化镁和氯化镧等助催化剂;在100~150℃、2MPa条件下合成DMC。
2.3常压非均相法
常压非均相法是由日本字部兴产公司开发的,采用钯系催化剂,以亚硝酸甲酯为催化反应的循环溶剂,在100℃、0.lMPa压力下,甲醇氧化羰基化合成碳酸二甲酯。该反应首先是一氧化碳与亚硝酸甲酯反应生成碳酸二甲酯和一氧化氮,第二步是一氧化氮与甲醇和氧气反应再生成亚硝酸甲酯。该工艺的主要副产物是草酸二甲酯,还有少量甲酸甲酯、二氧化碳、醋酸甲酯、甲缩醛和硝酸。对设备腐蚀严重,所用设备必须是耐强腐蚀特种不锈钢材质。将原料和主要含有一氧化碳、亚硝酸甲酯、氧、一氧化氮和甲醇的循环气混合,经预热后进入羰基化反应器。多管式固定床反应器内装有用活性炭吸附的Pdcl2/CuCl2催化剂。反应在100℃和0.1MPa的压力下进行。反应得到的产物经换热部分冷凝,再通过压缩和进一步冷凝。冷凝液进入草酸二甲酯回收塔分离回收草酸二甲酯。气相一部分循环使用,另一部分与补充的一氧化氮和氧一起加到亚硝酸甲酯再生器的底部。再生器是一个填充塔,操作压力为0.13MPa,温度为40℃。生成的亚硝酸甲酯作为原料气与再生器塔顶添加的甲醇接触之后进入羰基化反应器。从亚硝酸甲酯再生器底部出来的液相,进入脱水塔,脱水后的甲醇循环使用。从脱水塔顶部分离出来的甲酸甲酯和亚硝酸甲酯与草酸二甲酯回收塔顶部出来的物料一起进入甲酸甲酯回收塔回收甲酸甲酯。从草酸二甲酯回收塔釜出来的物料,进入碳酸二甲酯分离工段脱除甲醇后获得碳酸二甲酯产品,甲醇经回收塔回收后循环使用。与液相法比,采用固定床反应器,不需分离生成物和催化剂的装置,设备投资降低。使用亚硝酸甲酯合成DMC,反应在无水条件下进行,催化剂寿命增加。合成所需加入的氧气在亚硝酸甲酯再生器中反应,DMC合成器中不加入氧,所以CO2等副产物少;非氧气气氛使得爆炸危险性减小。但要副产3~5%的草酸二甲酯和1~3%的甲酸甲酯。
甲醇氧化羰基化生产碳酸二甲酯所用的原料为高纯度的一氧化碳和氧气;高纯一氧化碳的生产是由煤发生水煤气,经脱硫、铜洗、脱碳、变压吸附等工艺过程。高纯氧气原料需有一套空分装置。这些原料装置的投资是上述羰基化工艺流程装置投资的2~3倍。
3.其他一些合成方法
⑴二甲醚氧化羰基化法
直接以二甲醚和CO、O2反应合成DMC:
CH3OCH3+CO+1/2O2→(CH3O)2C
热力学上是可行的,且反应产物单一,没有水及其他副产物,进一步开发的关键是寻找合适的催化剂。不足之处是原料二甲醚与甲醇比较,价格较高。
⑵过氧化物氧化羰基化法
以正丁烷或异丁烷氧化成过氧化物,在一定的反应条件及催化剂存在下,过氧化物进行脱水、氧化羰基化反应可得DMC。该法实际上是以过氧化物代替甲醇氧化羰基化法中的氧气,避免了催化剂中毒,消除了催化剂失活现象,并且可以联产叔丁醇或MTBE。不足之处是副反应多,选择性差,生产成本较高。
⑶甲醇尿素法
NH2CONH2+2CH3OH→(CH3O)2CO+2NH3
该法由于反应很难进行,需要价格昂贵的催化剂、并加入络合剂束缚反应生成的氨,才能使反应向右进行;生产成本比酯交换法高约1000~1300元/吨;优点是可以与化肥厂联产,氨循环使用不受副产品的市场制约;目前国内外均无成熟的工业化装置。
⑷CO2和甲醇直接合成DMC
在催化剂作用下,甲醇和CO2直接合成DMC。
CO2+2CH3OH→(CH3O)2CO+H2O
华东理工大学研究了该法工艺。反应以镁粉作催化剂,在高压釜中、超临界条件下进行,甲醇既作原料又作溶剂。唯一的副产物是甲酸甲酯。与甲醇氧化羰基化法比较,不存在“爆炸极限”问题,相对安全,原料易得,有可能成为将来较有发展前途的方法之一,但目前收率只有2~3%,工业化前景需要10年以上。
⑸甲醇与CO电化学反应法
CO+2CH3OH→(CH3O)2CO+H2
该法在热力学上行不通,但是利用电能可以促使反应进行。美国的Cipris利用该法合成DMC获得成功,但目前成本较高。
⑹氯甲烷与碱金属碳酸盐反应法
2CH3Cl+K2CO3→(CH3O)2CO+2KCl
该法缺点是原料氯甲烷有毒,且价格较高,且有大量的副产氯化钾。以上六种合成方法,正处于起步研究阶段,距工业化尚有很长一段路。与反应精馏酯交换法相比仍具有投资大、成本高等不足。
4.工艺技术比较
近年来某企业对二氧化碳与环氧丙烷合成碳酸丙烯酯的技术做了重大改进使能耗大幅下降,收率提高;又对酯交换反应精馏塔做了重大改进,使反应的转化率和选择性都达到了99%以上,对过程进行了优化能耗降低40~50%,使生产成本降到了全世界同规模最低。从二氧化碳为起始原料的酯交换法生产碳酸二甲酯的技术路线是最具有竞争力的。
年产10000吨DMC投资及生产成本比较(单位:万元)
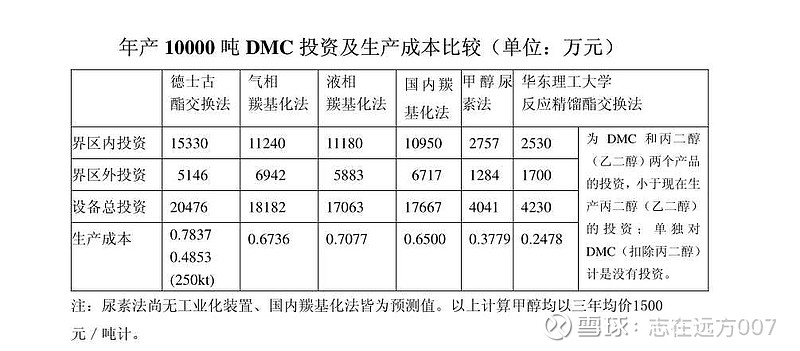
注:尿素法尚无工业化装置、国内羰基化法皆为预测值。以上计算甲醇均以三年均价1500元/吨计。
从上述几个生产碳酸二甲酯工艺流程的比较,可以清楚的看到,酯交换法所需的原料来源方便、原料成本低、对设备无腐蚀、总设备投资小,设备投资在年产1000吨时是羰基化法的l/5、在年产10000吨时是羰基化法的1/4;生产过程安全易控、操作方便。酯交换法综合成本低,扣去联产丙(乙)二醇后成本2478元/吨(综合成本4132元/吨),羰基化法生产成本6736~7077元/吨,甲醇尿素法生产成本3779元/吨。酯交换法生产中基本上是全封闭的、过程无三废排放,且可以充分利用化工厂、酒厂、石灰厂等排放的二氧化碳废气,既变废为宝,又净化了环境;社会资源占用率减少41.5%;是一条绿色环境友好工艺。甲醇氧化羰基化法,因生产原料一氧化碳时产生大量固体废料;同时过程中有废水产生,副产3~5%的草酸二甲酯,国内目前尚无用途(日本近年来大量的研究是用草酸二甲酯酯交换法生产碳酸二甲酯),暂时只能作为废物处理,污染环境。羰基化反应往往在其原料的爆炸极限区域内进行,因此对设备的安全和自动化控制要求比较高。因有酸性副产物生成,腐蚀设备,工艺流程长、设备投资大;原料路线长、成本高。因此华东理工大学的反应精馏酯交换法具有非常显著的经济优势。酯交换法虽然具有很大的优越性,但其发展规模受到副产物丙二醇或乙二醇的制约;目前国内丙二醇的总需求量约16万吨,总生产能力约3万吨,尚缺口13万吨,乙二醇的总需求量约256万吨,尚缺口146万余吨。因此,近期酯交换法生产碳酸二甲酯从环氧丙烷为起始原料的最大能力约15.5万吨,从环氧乙烷为起始原料的最大能力约229万吨;全部取代现有的丙二醇(乙二醇)工艺后,其最大生产能力也只能有420万吨左右。由此可以看到,碳酸二甲酯作为一个有机合成的新基石,在不太久的将来作为象甲醇一样的基础化工原料,发展甲醇氧化羰基化法和甲醇尿素法要在500万吨以上的市场才有竞争力(因为丙二醇和乙二醇的市场发展也很快,年均增长6%)。长远来看(十年之后),二氧化碳直接合成DMC的路线值得关注和开发。